Artificial intelligence (AI) seems to be permeating everything we do, from the innocuous to the incomprehensibly complex. It’s hard to find an industry that hasn’t identified, and started implementing ways, to supercharge operations and strategy using AI.
In the energy industry, AI is beginning to revolutionize software, hardware, and system integration encompassing downstream, midstream, upstream oil and gas among other sectors.
The explosive growth is driven by the increasing adoption of AI technologies for optimizing operations, improving safety, and adding a measurable degree of certainty in decision-making.
North America
North America is a leader in the adoption of AI in the energy industry. The region accounts for slightly over 38% of the global AI energy market. Why?
Major energy companies and tech giants are developing AI solutions – primarily in Canada and the United States. Unconventional methods of oil and gas production have also driven the adoption of AI technologies to optimize performance.
In 2023, the oil and gas market in North America was valued at approximately $2.8 billion. It is projected to rise to $5.96 billion by 2028, at a compound annual growth rate of 13.3% from 2023 to 2028.
Key Applications and Technologies
1. Enhanced Oil Recovery
Enhanced Oil Recovery (EOR) refers to a class of techniques used to increase the amount of crude oil that can be extracted from an oil field. Typically, after traditional methods, EOR helps extract a significant amount of oil trapped in a reservoir that can’t be recovered.
AI can often help with:
- Reservoir characterization to get accurate characterization, including porosity, geological features, permeability, and fluid properties, to calculate the precise reservoir simulation and performance prediction
- Intelligent reservoir monitoring and management for optimized production.
- Selecting the most suitable EOR techniques based on reservoir conditions improves recovery rates.
- Optimizing EOR operations to maximize oil recovery while minimizing operational costs.
The benefits don’t end there; however, with machine learning and deep learning, genetic algorithms, digital twins, AI and IoT integration, companies can fine-tune the extraction process to a high degree.
2. Predictive Maintenance
Unexpected maintenance issues are a common occurrence due, in part, to the complexity and scale of oil and gas production in North America. Machine learning algorithms are now being deployed to analyze data from sensors and sift through historical records.
AI brings insights that help predict equipment failures before they happen. This technology can be applied in the field as well to monitor equipment performance and detect issues early. This helps reduce downtime and maintenance costs.
3. Drilling Optimization
AI can be leveraged to provide real-time data analysis and precise drill-bit steering, reducing non-productive time, improving safety, and enhancing drilling efficiency. These systems can be trained to detect anomalies and abnormal conditions and take immediate action to correct errors.
Additionally, the algorithms can analyze historical data to create decision-making systems, such as drill bit selection and techniques.
4. ESG (Environmental, Social and Governance) Goals
The Internet of Things (IoT) promises to be a game changer for companies looking to meet their ESG requirements. Machine learning algorithms can process data from a wide variety of sources, such as geological surveys and sensors, to monitor and detect things such as leaks and emissions.
Most people feel that we are still behind on this issue and the new technologies are part of vindicating that sentiment. This leap forward should be viewed as an opportunity for oil and gas companies to coordinate timely interventions and adhere to environmental regulations.
These companies hope to optimize energy usage in oil and gas operations to reduce their carbon footprint significantly. AI can also help predict energy demand and help identify opportunities for integrating renewable energy sources into the process.
5. Digital Twins
A digital twin is a virtual replica of a physical asset, system, or process, and oil and gas companies are using them in conjunction with real-time data gathering and simulations to mirror the performance, condition, and behavior of its real-world counterpart.
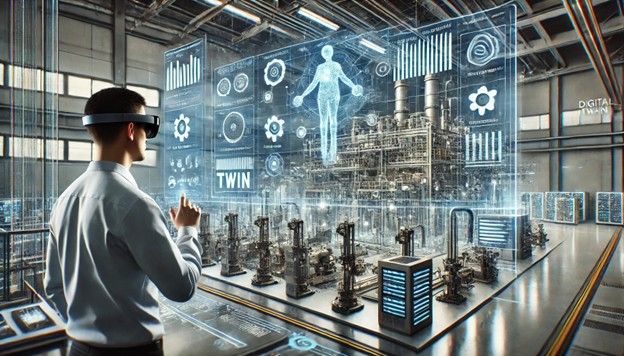
Digital twins are often designed for real-time monitoring and diagnostics, predictive maintenance, operations optimization, asset lifecycle management, and remote monitoring and control.
For example, BP has implemented digital twins for its offshore platforms, Chevron uses them to optimize the performance of its refineries, and Shell has deployed digital twins for its deepwater operations in the Gulf of Mexico.
6. Logistics
AI is being extensively applied to logistics in several ways, with interesting results:
- AI provides insights into demand forecasting, inventory management, and logistics planning. Predictive analytics can anticipate demand fluctuations, allowing companies to adjust their operations accordingly.
- Analysis of real-time data from sensors and historical data is leveraged both off- and on-shore to maintain optimal inventory levels and reduce risks of overstocking or understocking.
- AI-driven demand planning and forecasting tools analyze market trends, external factors, and data to predict future demand and plan procurement and logistics accurately.
- AI can automate procurement processes by analyzing supplier performance, market conditions, and historical data.
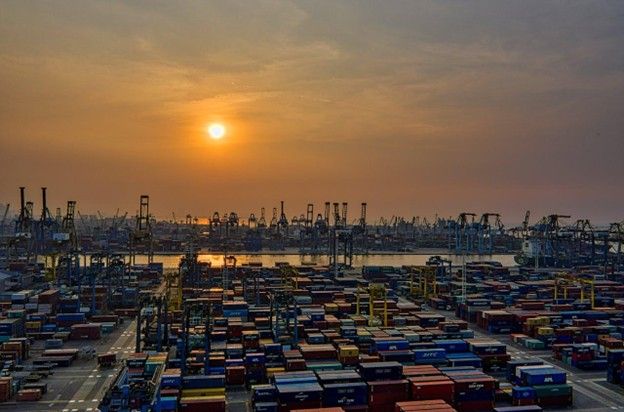
Almost every aspect of logistics, from monitoring to route optimization, can benefit from powerful AI solutions.
Future Prospects
According to an extensive report by Research and Markets, the integration of AI in the oil and gas industry is expected to continue growing, with a focus on:
- Sustainability – AI is expected to play a crucial role in reducing the environmental footprint of oil and gas operations by optimizing resource use and minimizing waste.
- Safety – AI can enhance safety by providing real-time monitoring and identifying potential hazards.
- Operational efficiency – AI is already streamlining logistics and refining decision-making for smoother operations.
- Greater automation – Companies will increasingly automate as many processes as they can for efficiency gains.
- Enhanced predictive analytics – To anticipate needs and meet them accurately will help with demand forecasting and inventory management.
- Carbon Capture and Storage – What was once a hypothetical technology is now seeing increased investment and breakthroughs that show its true potential could be world-changing.
The full impact of artificial intelligence is still unfolding, and companies need to keep an eye on the market as AI technologies advance, to make full use of these new capabilities.
Looking for a digital engineering partner for your next project?
Vista Projects is an integrated engineering services firm able to assist with your energy project. With offices in Calgary, Alberta, Houston, Texas, and Muscat, Oman, we help clients tailor engineering phases for the unique needs of their projects. Contact us today!
source https://www.vistaprojects.com/the-role-of-artificial-intelligence-in-energy-exploration-in-2025/
source https://vistaprojects2.blogspot.com/2024/12/the-role-of-artificial-intelligence-in.html